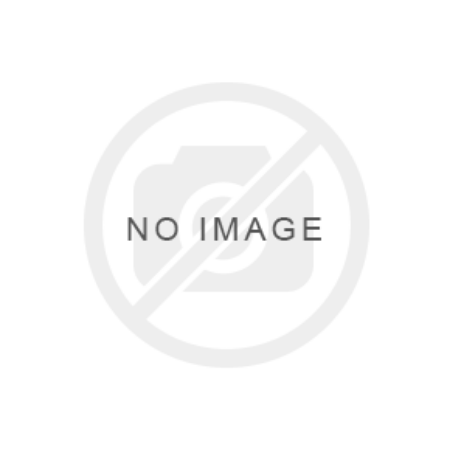
Introduction
In an ever-evolving world, construction methods need to constantly adapt and develop. Concrete remains one of the most widely used construction materials due to its versatility, strength, affordability, durability, and flexibility. It is used in all types of buildings—from residential homes to multi-story office blocks—and infrastructure projects like roads and bridges. Concrete is essential for constructing foundations, columns, beams, slabs, and other load-bearing components. This comprehensive report will cover the following topics:
1. What is Concrete?
2. Types of Concrete and Their Uses
3. Conclusion
What is Concrete?
Definition:
Concrete is an artificial stone-like material created by mixing a binding material (cement or lime) with aggregates (sand, gravel, stone, brick chips, etc.), water, and sometimes admixtures in specific proportions. The strength and quality of concrete depend on the mixing proportions of these ingredients.
Composition:
- Binding Materials: The primary element, typically cement or lime.
- Aggregates: Includes fine aggregates like sand and coarse aggregates such as gravel or stone chips.
- Water: Reacts chemically with the cement (hydration) to form a hard mass.
- Admixtures: Optional additives like pozzolana to modify the properties of concrete.
When these ingredients are mixed in the required proportions, the cement and water form a paste that coats the aggregates. This paste hardens to form a rock-like mass.
Properties and Advantages:
- Strength and Durability: Concrete is strong, durable, and can withstand various environmental conditions.
- Versatility: It can be molded into different shapes and sizes.
- Cost-Effectiveness: Concrete is affordable and low-cost.
- Quick Construction: Allows for reliable and high-quality fast-track construction.
- Resilience: Structures built with concrete can withstand natural disasters like earthquakes, hurricanes, and tornadoes.
Types of Concrete and Their Uses
1. Lime Concrete:
- Components: Lime, surki, and khoa or stones.
- Uses: Mainly in foundations and terrace roofing.
- Advantages: More workable, cheaper, lower heat of hydration, good resistance to fire and sulfate attack.
- Disadvantages: Lower strength, less durability, susceptible to frost attack.
2. Cement Concrete:
- Components: Cement, sand, brick chips, or stone chips.
- Uses: Structural applications (beams, columns, slabs, foundations) and non-structural applications (paving, curbing).
- Advantages: Strength, durability, fire resistance.
- Disadvantages: Heavy material, susceptible to cracking, can be damaged by extreme weather.
3. Reinforced Cement Concrete (RCC):
- Components: Cement concrete with steel reinforcements.
- Uses: Provides enhanced tensile strength, used in structures subjected to high tensile forces.
- Advantages: Stronger and more durable than plain cement concrete.
4. Dry Ready Mix Concrete:
- Description: Pre-mixed dry ingredients, just add water.
- Uses: Small home projects.
- Advantages: Easy to mix, convenient for small-scale projects.
5. Ready Mix Concrete:
- Description: Pre-mixed wet concrete, delivered to the site.
- Uses: Larger home projects or commercial projects.
- Advantages: Consistent quality, convenient, reduces labor costs.
6. Bulk Dry Materials:
- Description: Purchase of dry materials in bulk.
- Uses: Custom concrete mixes for specific needs.
- Advantages: Cost-effective for large projects.
7. Transit Mix Concrete:
- Description: Concrete mixed in transit using concrete trucks.
- Uses: Large-scale construction projects.
- Advantages: Continuous pour, fewer seams, stronger concrete.
8. Regular Concrete:
- Description: Traditional weight and strength concrete.
- Uses: General construction purposes.
- Advantages: Widely available, versatile.
9. High-Strength Concrete:
- Description: Compressive strength over 6000 psi.
- Uses: High-load structures.
- Advantages: Greater strength and durability.
10. Stamped Concrete:
- Description: Decorative concrete with patterns resembling natural stones.
- Uses: Driveways, patios, interior floors.
- Advantages: Aesthetic appeal, cost-effective.
11. High-Performance Concrete:
- Description: Improved properties over regular concrete.
- Uses: Specialized applications requiring enhanced performance.
- Advantages: Increased strength, durability, workability.
12. Self-Consolidating Concrete:
- Description: High workability concrete that compacts under its own weight.
- Uses: Areas with dense reinforcement.
- Advantages: No vibration needed, high flowability.
13. Vacuum Concrete:
- Description: Excess water removed using vacuum.
- Uses: Rapid construction.
- Advantages: Faster curing, higher early strength.
14. Shotcrete:
- Description: Mortar or concrete sprayed at high speed onto surfaces.
- Uses: Structural and non-structural parts of buildings.
- Advantages: Versatile application, strong bond.
15. Roller-Compacted Concrete:
- Description: Placed and compacted with heavy rollers.
- Uses: Excavation and filling.
- Advantages: High density, strong monolithic block.
16. Glass Concrete:
- Description: Recycled glass used as aggregate.
- Uses: Decorative concrete, countertops, flooring.
- Advantages: Sustainable, unique appearance.
17. Asphalt Concrete:
- Description: Mix of aggregates and asphalt.
- Uses: Roads, parking lots, airports.
- Advantages: Durable, flexible.
18. Rapid Strength Concrete:
- Description: Gains strength within a few hours.
- Uses: Road repairs, quick construction.
- Advantages: Quick formwork removal, fast construction.
19. Polymer Concrete:
- Description: Aggregates bound with polymer instead of cement.
- Uses: Specialized applications.
- Advantages: Reduced voids, stronger bond.
20. Limecrete:
- Description: Cement replaced by lime.
- Uses: Floors, domes, vaults.
- Advantages: Sustainable, easy to clean, cool in hot weather.
- Disadvantages: Not as strong as cement, more expensive.
21. Light-Transmitting Concrete:
- Description: Concrete with lower density, utilizing lightweight aggregates.
- Uses: Steel structure protection, long-span bridge decks.
- Advantages: Lightweight, protective.
Conclusion
Concrete remains a fundamental material for building and construction works due to its versatility, strength, and durability. Understanding the different types of concrete and their specific applications allows for optimized use of this material in various projects. By selecting the appropriate type of concrete, engineers and builders can ensure the success and longevity of their construction engagements. As the construction industry continues to evolve, so too will how concrete is utilized, paving the way for innovative and sustainable building practices.
Pre-stressed concrete is a type of concrete where initial compression is applied before any external load is introduced. This initial compression is achieved using high-strength steel wires or alloys, known as ‘tendons,’ embedded within the concrete. The primary goal of this compression is to counteract tensile stresses caused by external loads, enhancing the concrete's performance and durability during its service life.
Why is Prestressed Concrete Required?
Concrete, while excellent in compression, is inherently weak in tension. When external loads are applied, a tension zone forms at the bottom of the concrete structure, leading to elongation and cracking. Traditionally, steel reinforcement bars are added to the bottom section to resist these tensile forces and prevent cracking. This method is effective for regular reinforced concrete (RC) structures but is not sufficient for megastructures with large beam spans, such as flyovers or iconic bridges like the Gateway Bridge in Australia, Incheon Bridge in South Korea, and the Ringhals nuclear reactor in Sweden, where external loads are significantly high.
In such cases, traditional RC structures would require beams with considerable depth, which could obstruct clearance under structures like bridges. Prestressed concrete offers a solution by introducing initial compression, which counteracts the tensile forces, thus preventing cracking and reducing the required beam depth.
How Does Prestressed Concrete Work?
The working mechanism of prestressed concrete involves the insertion of high-tensile strength steel wires into the concrete beam section. These wires are stretched and anchored before the concrete is poured. Once the concrete has cured, the tendons are released, causing them to try to return to their original length. This action transforms the tensile stresses in the tendons into compressive stresses within the concrete.
This process generates two primary forces on the beam:
1. Internal Prestressing Force: Introduced by the pre-stretched tendons.
2. External Forces: Including dead loads (permanent/static loads) and live loads (temporary/dynamic loads).
These forces must counterbalance each other to maintain structural integrity. By examining the moment diagram, engineers can design the structure to ensure these forces are effectively managed.
Materials Used in Prestressed Concrete
According to the American Association of State Highway and Transportation Officials (AASHTO), prestressed concrete requires high-strength materials. These include seven-wire strands, high-strength steel wire, or specific alloys. Additionally, the concrete used must have a minimum 28-day cylinder strength of 5000 psi. This high-strength concrete is essential to prevent cracking or failure under the stress induced by the tendons. It also offers higher resistance to tension and shear forces, making it ideal for prestressed concrete applications.
High-strength concrete has several advantages:
- Reduced Susceptibility to Shrinkage Cracks: High-strength concrete experiences less shrinkage, minimizing the risk of cracks developing.
- Higher Modulus of Elasticity: This property means the concrete deforms less under stress, improving its overall performance.
- Smaller Creep Strain: Reduced long-term deformation under sustained load ensures that the structure maintains its intended shape and function over time.
Applications of Prestressed Concrete
Prestressed concrete is used in various structural applications where high strength and durability are required. Some common applications include:
- Bridges: Prestressed concrete allows for longer spans and reduced beam depths, which is essential for bridge construction.
- Flyovers and Overpasses: These structures benefit from the reduced beam depth and enhanced load-carrying capacity of prestressed concrete.
- High-rise Buildings: Prestressed concrete provides the necessary strength to support the heavy loads and long spans required in skyscrapers.
- Industrial Structures: Structures that require large open spaces, such as warehouses and factories, benefit from the use of prestressed concrete.
- Parking Structures: The enhanced load-bearing capacity and reduced maintenance requirements make prestressed concrete ideal for multi-level parking facilities.
Advantages of Prestressed Concrete
Prestressed concrete offers several advantages over traditional RC structures:
- Increased Load-Bearing Capacity: The initial compression allows the concrete to withstand higher loads without cracking.
- Reduced Structural Depth: Prestressed concrete beams can be shallower, providing more clearance under structures.
- Enhanced Durability: The use of high-strength materials and the reduction of tensile stresses result in longer-lasting structures.
- Improved Performance Under Dynamic Loads: Prestressed concrete is better suited to resist vibrations and impacts, making it ideal for dynamic load applications.
- Cost-Effective: Despite the higher initial costs, the reduced maintenance and longer lifespan of prestressed concrete structures often result in lower overall costs.
Disadvantages of Prestressed Concrete
While prestressed concrete offers numerous benefits, it also has some disadvantages:
- Complex Design and Construction: The design and construction processes for prestressed concrete are more complex and require specialized knowledge and equipment.
- Higher Initial Costs: The materials and labor involved in prestressing can be more expensive than traditional RC structures.
- Limited Repair Options: Repairs to prestressed concrete structures can be challenging, as the tendons are under high tension.
- Sensitivity to Environmental Conditions: The tendons can be susceptible to corrosion if not adequately protected, requiring careful attention to environmental factors.
Prestressed concrete represents a significant advancement in construction technology, providing a robust solution for structures subjected to high external loads. By introducing initial compression through high-strength tendons, prestressed concrete effectively counteracts tensile stresses, preventing cracking and enhancing structural performance. This technology is particularly beneficial for megastructures with large spans, where traditional RC structures would be impractical.
The use of high-strength materials and the careful design of prestressed concrete elements ensure that these structures can withstand significant forces while maintaining their integrity and longevity. As a result, prestressed concrete continues to be a vital component in modern construction, providing engineers with the tools to create safer, more efficient, and more durable structures.
By understanding the principles and applications of prestressed concrete, engineers can effectively address the challenges posed by large-scale construction projects and contribute to the development of innovative and resilient infrastructure.
Retaining walls serve multiple critical purposes in construction, such as protecting river banks from erosion, retaining loose soil around foundation trenches, isolating foundations from adjacent soils, and increasing the soil's bearing capacity. Among the various methods of constructing retaining walls, pile foundations stand out due to their versatility and ability to handle different load types and soil conditions. This article explores the types of piles, their applications, and their advantages and disadvantages, offering a comprehensive overview of this crucial aspect of civil engineering.
Types of Piles and Their Applications
Load Bearing Piles:
Load-bearing pile foundations are primarily used to transfer vertical loads from the structure to the soil. They transmit these loads through weak soil layers to more stable soil layers. Depending on the load transfer mechanism, they can be further classified into end-bearing piles and friction piles.
End Bearing Piles:
End-bearing piles transfer loads through their lower tip, which rests on a strong layer of soil or rock. They act like columns, safely transmitting the load to the firm layer. The total capacity is calculated by the pile tip area and the bearing capacity of the soil at that depth. This type of pile is particularly useful when the upper layers of soil are too weak to support the structure, but a strong layer exists at a greater depth.
Friction Piles:
Friction piles transfer loads through the frictional force between the pile surface and the surrounding soil. The entire surface of the pile can work to transfer the load, depending on the soil strata. The capacity is determined by the pile surface area and the safe friction force per unit area. Friction piles are ideal for situations where there is no strong layer of soil at a reasonable depth, and the load needs to be distributed over a larger area through friction.
Soil Compactor Piles:
Unlike other pile foundation types, soil compactor piles do not carry any direct loads. Instead, they are driven into the ground at close intervals to increase the soil's bearing capacity by compacting it. This compaction improves the soil's density and reduces its settlement under load.
Types of Piles Based on Materials and Construction Methods
Piles can be divided into displacement piles and non-displacement (replacement) piles. Displacement piles displace soil as they are driven into the ground, while replacement piles involve removing soil and filling the space with concrete or pre-cast piles. Based on the material and installation process, piles are classified into timber, concrete, and steel piles.
Timber Piles:
Timber piles, often used underwater, last about 30 years and can be rectangular or circular. They are cost-effective and easy to install but require preservatives for durability and are not suitable for end-bearing applications.
Concrete Piles:
Concrete piles are either pre-cast or cast-in-place. Pre-cast piles are reinforced with steel and cured before use, while cast-in-place piles involve boring soil and filling it with concrete. Both types offer high strength and resistance but come with logistical challenges.
- Pre-cast Concrete Piles:
Pre-cast concrete piles are cast in a pile yard and cured before transportation to the construction site. They are usually reinforced with steel to prevent breakage during handling and driving. Pre-cast piles can be circular or rectangular and offer high resistance to chemical and biological deterioration. However, their fixed length makes them less adaptable to on-site conditions, and they require heavy equipment for installation.
- Cast-in-Place Concrete Piles:
Cast-in-place concrete piles are constructed by boring a hole into the ground and filling it with freshly mixed concrete. This method allows for greater flexibility in pile length and avoids the need for heavy lifting equipment.
However, it requires careful quality control and is challenging to execute in areas with high groundwater flow.
Steel Piles:
Steel piles, such as I-section or hollow pipe piles, are filled with concrete and can reach greater depths. They are easy to splice and carry heavy loads but are prone to corrosion and are more expensive.
- I-Section Piles:
I-section piles are typically driven into the ground to support heavy loads. They are efficient for deep foundations and can penetrate hard soil layers. However, they require anti-corrosion treatments to ensure longevity.
- Hollow Piles:
Hollow steel piles are often filled with concrete to increase their load-bearing capacity. They are versatile and can be used in various soil conditions but are also susceptible to corrosion if not properly treated.
Advantages and Disadvantages of Different Pile Types
Timber Piles:
- Advantages:
- Readily available in regular sizes.
- Economical and easy to install.
- Low possibility of damage and can be cut to desired lengths.
- Disadvantages:
- Longer lengths may not be available.
- Difficult to drive in hard soil strata.
- Require treatment with preservatives for durability.
- Not suitable for end-bearing applications.
Pre-cast Concrete Piles:
- Advantages:
- High resistance to chemical and biological cracks.
- High strength and controlled quality.
- Can be driven underwater and loaded immediately.
- Disadvantages:
- Fixed length makes them less adaptable.
- Requires heavy and expensive equipment to drive.
- Potential for breakage during handling and driving.
Cast-in-Place Concrete Piles:
- Advantages:
- Lightweight shells are easy to handle.
- Length can be varied easily.
- No possibility of breaking during installation.
- Greater flexibility in on-site conditions.
- Disadvantages:
- Requires careful supervision and quality control.
- Needs sufficient space on site for material storage.
- Challenging to construct with heavy underground water flow.
The bottom of the pile may not be symmetrical.
Steel Piles:
- Advantages:
- Easy to install and can penetrate hard soil layers.
- Can carry heavy loads and are easy to splice.
- Reach greater depths compared to other types.
- Disadvantages:
- Prone to corrosion.
- Expensive compared to other types.
- Possibility of deviation while driving.
Pile foundations play an essential role in modern construction, offering solutions for various challenges related to soil and load-bearing capacity. From load-bearing piles that transfer vertical loads to friction and soil compactor piles that enhance soil stability, the different types of piles each serve specific functions. The choice of material, whether timber, concrete, or steel, further influences the performance and suitability of the piles for different applications. Understanding the advantages and limitations of each type of pile foundation is vital for engineers to make informed decisions that ensure the stability and longevity of structures.
By comprehending these key aspects of pile foundations, engineers can effectively address specific construction challenges and contribute to the successful execution of various construction projects.